Achieving EMI Agency Compliance for a Medical Device

The Fortune 500 client approached Re:Build AppliedLogix with an urgent request to critically assess their production intent imaging subsystem design that was failing EMI compliance testing for radiated emissions levels. The failing subsystem was a vital element within a new product platform they were developing and readying for launch.
Their internal engineering staff along with the subcontractor’s engineering team (who designed the imaging subsystem) had worked for many months but were struggling to identify and remedy the design shortfalls causing the EMI emissions. The subcontractor had attempted several PCBA design spin iterations, all without success. The client team and subcontractor were both under intense pressure from senior management to solve the problems ASAP and get the product platform certified and released into full production.
Mechanical Design of a Cabinet

AppliedLogix was tasked with developing a customer-scalable Biomass Dryer Cabinet that could be readily (re)configured to meet each customer’s unique requirements. The core concept was based on developing vertically stackable assemblies that would be supplied to the end customer via a complete set of drawings and instructions. Further, the stackable units needed to be constructed from readily available building materials.
Spaceborne Electronic Enclosure Mechanical Design
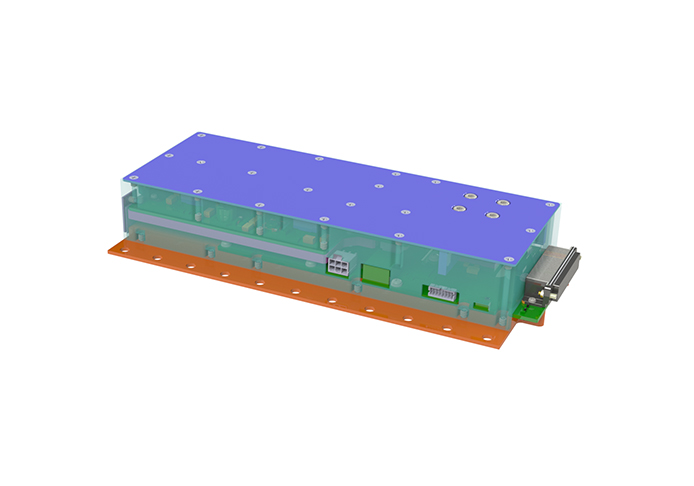
Re:Build AppliedLogix was tasked with developing an electronics enclosure that would withstand the thermal and mechanical stresses, including the vibrational loading during launch, that results from being placed in a zero-G earth orbit aboard a space launch vehicle. The enclosure design needed to support multiple interconnected printed circuit board (PCB) assemblies, while meeting stringent electromagnetic compatibility (EMC) standards, and providing robust connector mounting for customer harnessing between modules and test apparatus.
Custom Data Acquisition and Logging Module
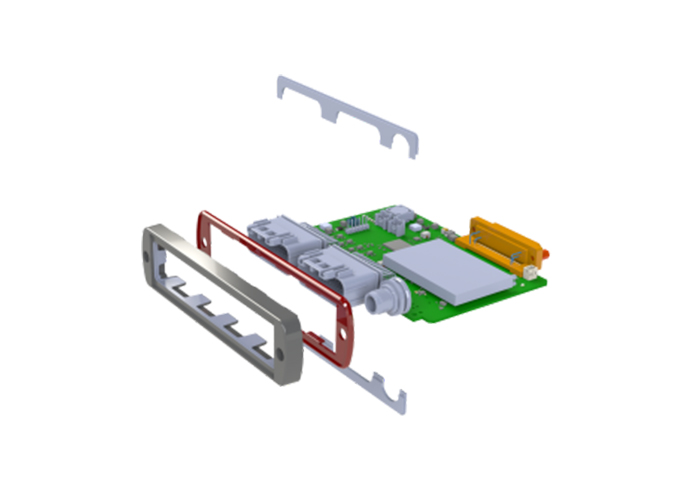
An established company within the electric vehicle material handling space approached Re:Build AppliedLogix with a need to expand the capabilities of their existing commercial-of-the-shelf (COTS) 4-channel CAN Bus based data logger. They needed a solution that would support the capture and recording of a wide range of operational characteristics of their vehicles. Their existing data logger solution lacked sufficient support for their unique mix and quantity of signal conditioning and capture requirements.
FPGA Communications Module enhances Industrial Instrumentation Equipment
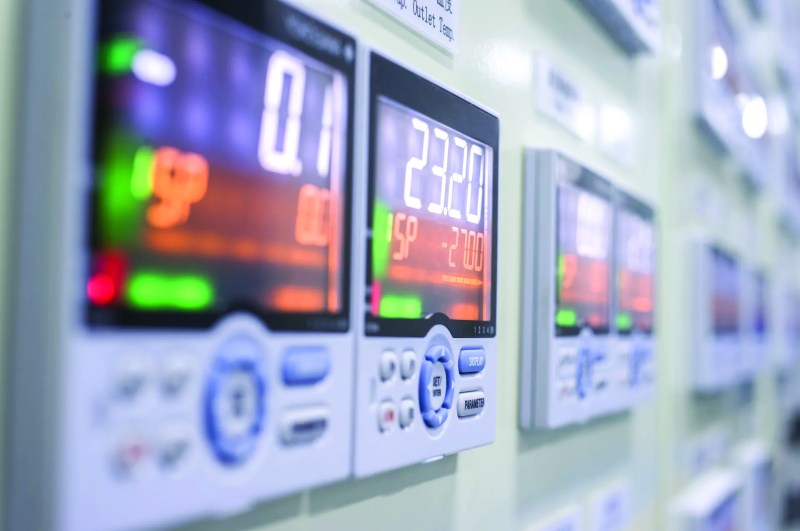
Our client manufactures industrial instrumentation equipment that plays a key role within the semiconductor fabrication process. During their product roadmap planning, they identified an expanded set of features and functionality including the need to share data between separate pieces of equipment on the factory floor. With their internal development team stretched too thin, they turned to AppliedLogix to provide the expertise required to design and deliver the FPGA-based communications enhancements that were needed.
Design and Development of a Custom, 6-DOF Robotic Arm
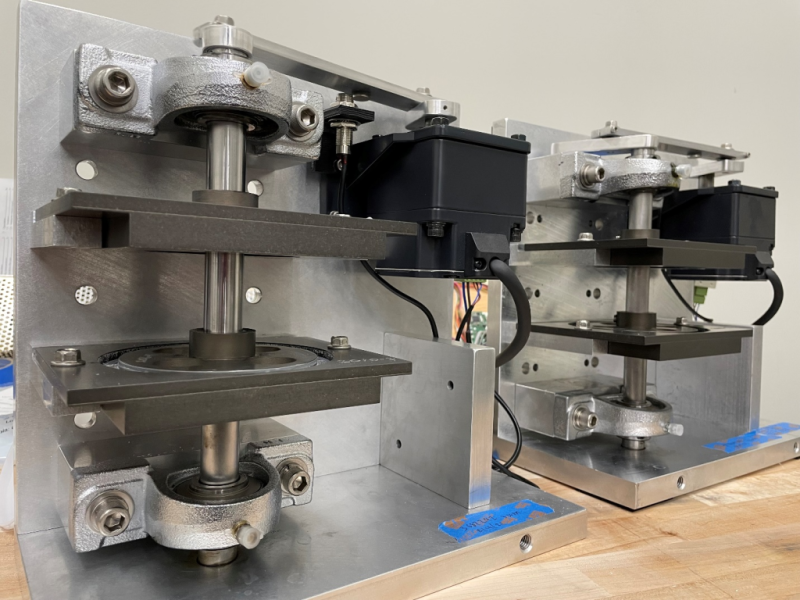
Re:Build AppliedLogix was tasked with developing a full custom six degree of freedom (6-DOF) robotic arm for an outdoor agricultural application. The available commercial off the shelf (COTS) 6-DOF arms were carefully assessed and found to be unable to meet the environmental requirements nor the volume manufacturing pricing goals. The application dictated unique design requirements for the arm’s segment lengths and the orientation of the joints relative to one another. Additionally, the robotic arm was required to achieve an IP65 environmental rating over 10 million operational cycles. The harsh environment dictated that the materials and coatings selection needed to be inert for any exposed surfaces where wear was expected during normal operation. The robotic arm needed to operate on DC voltage and the servo actuators needed to operate at aggressive speeds and accelerations while moving a 3kg payload. In the event of a power loss or an emergency stop, position needed to be maintained and motion stopped within specified time to meet safety requirements. Additionally, the stopped unpowered robotic arm needed to support manual repositioning and then hold in place without damage.